
PVC60 degree plastic particles are revolutionizing the materials industry, offering a unique blend of durability, environmental resistance, and mechanical strength. These high transparent, environmentally-friendly raw materials from Zhenhan are designed to meet a wide range of applications across multiple industries.
Understanding PVC60 Degree Plastic Particles
PVC60 degree plastic particles are a type of polyvinyl chloride (PVC) material characterized by their specific physical properties that make them suitable for numerous uses. Composed mainly of ethylene and chlorine, these particles stand out due to their ability to endure higher temperatures while maintaining transparency and robustness.
When compared to other types of plastic particles, such as polypropylene or polyethylene, PVC60 particles offer superior tensile strength, greater flexibility, and enhanced resistance to UV radiation and chemicals. This places them ahead in terms of performance under harsh conditions.
The development of PVC60 degree plastic particles marks a significant advancement in material science. Initially engineered to address limitations found in standard PVC materials, ongoing research and innovations have further refined its formulation to optimize performance metrics without compromising safety or sustainability.
Key Benefits of PVC60 Degree Plastic Particles
The standout feature of PVC60 degree plastic particles is their unparalleled durability, making products last significantly longer even when exposed to demanding environments. This material’s resistance to UV radiation, chemical interactions, and temperature variances ensures extended longevity and reliability.
Moreover, these particles exhibit remarkable mechanical properties, including high tensile strength and excellent flexibility, which means they can withstand deformation and stress better than many alternatives. These attributes contribute not only to the durability but also to the functionality of end products.
Applications in Various Industries
Given their exceptional properties, PVC60 degree plastic particles find diverse applications. In the construction industry, they are utilized in pipes, fittings, and various building materials, offering enhanced structural integrity and resistance to wear and tear.
The automotive sector benefits greatly from these materials through their use in both interior and exterior components. Their resilience to environmental factors ensures enduring performance and aesthetic retention over time.
In electronics, PVC60 particles serve in casings, connectors, and insulation materials, providing reliable protection against mechanical damage and thermal stress. Consumer goods like toys, household items, and packaging also incorporate these particles, favoring long-lasting utility and safety.
Technical Specifications and Standards
Adherence to industry standards and certifications underscores the quality and reliability of PVC60 degree plastic particles. They typically conform to ASTM, ISO, and RoHS norms, ensuring compatibility and safety across different applications.
From a technical standpoint, these particles boast notable properties such as a melting point around 148 degrees Celsius, a density of approximately 1.38 g/cm³, and an impressive hardness rating. When pitted against other durable materials, their performance on key metrics often surpasses expectations.
Manufacturing and Processing Techniques
The versatility of PVC60 degree plastic particles extends to their manufacturing processes. Through injection molding and extrusion techniques, manufacturers can create complex shapes and structures with precise specifications. Blending and compounding with other materials can further tailor these particles to meet specific needs.
Best practices in handling and processing include maintaining optimal temperature control and employing appropriate mold designs to ensure uniformity and prevent defects. Comprehending these nuanced steps helps maximize the material's potential.
Case Studies and Real-World Examples
Numerous companies have successfully integrated PVC60 degree plastic particles into their product lines, reporting marked improvements in performance and longevity. For instance, a leading automotive manufacturer noted a significant reduction in component failure rates after switching to PVC60 materials, highlighting their robustness and reliability.
Environmental Considerations and Sustainability
Lifecycle analyses reveal that PVC60 degree plastic particles offer promising prospects for sustainability. While their production requires robust energy inputs, the reduced need for frequent replacements and maintenance contributes to lower overall environmental impacts. Recycling options further enhance their eco-friendliness, allowing for the efficient reutilization of resources.
Cost-Benefit Analysis
Investing in PVC60 degree plastic particles might require a higher initial expenditure; however, the long-term savings through reduced repair and replacement costs often justify this investment. A comparative analysis shows favorable ROI outcomes, particularly where durability and performance are critical.
Future Trends and Innovations
The future looks bright for PVC60 degree plastic particles with emerging technologies continually broadening their applicability. Research indicates potential new markets such as medical devices and advanced consumer electronics leveraging the unique advantages of this material.
Expert Tips for Maximizing Durability
To fully harness the benefits of PVC60 degree plastic particles, adherence to certain best practices is crucial. Avoid exposure to solvents that may degrade the material, ensure proper installation techniques, and regularly maintain the finished products to catch and rectify early signs of wear. Addressing common issues, such as cracking or discoloration promptly, preserves the functional integrity over extended periods.
In conclusion, PVC60 degree plastic particles are setting a new benchmark for durability and performance in the plastics industry. Their comprehensive benefits across varied sectors, coupled with promising future trends, position them as an indispensable material for innovative and sustainable solutions.
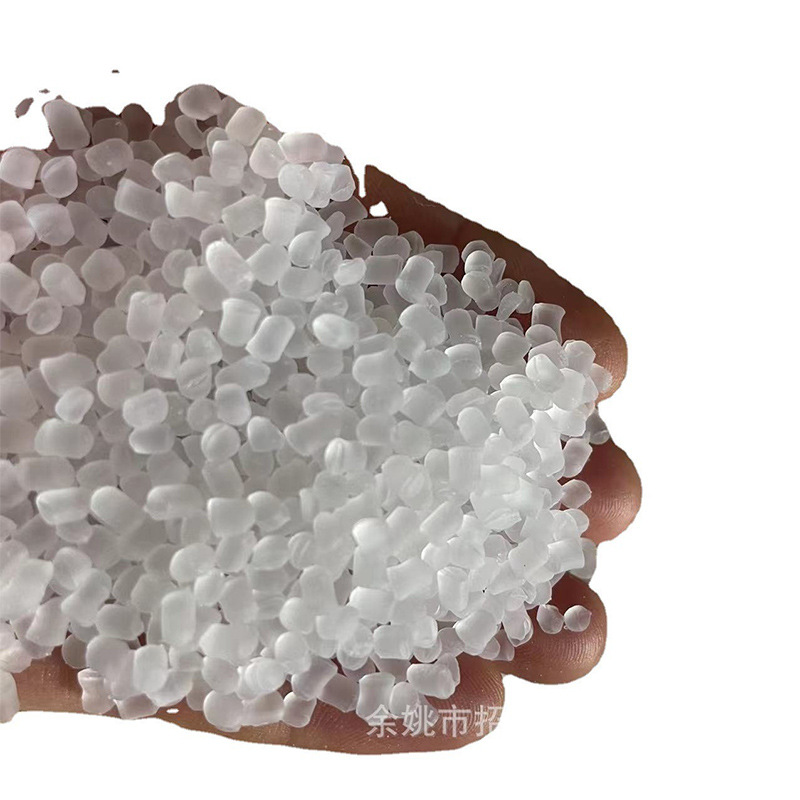